www.industry-vietnam.com
02
'10
Written on Modified on
Consistent communication interfaces for Baldor
Baldor Electric Company has upgraded its range of smart drives with HMS. This range is now able to communicate with a PLC, it is much more open to communication standards and its communication interfaces are consistent throughout the entire range.
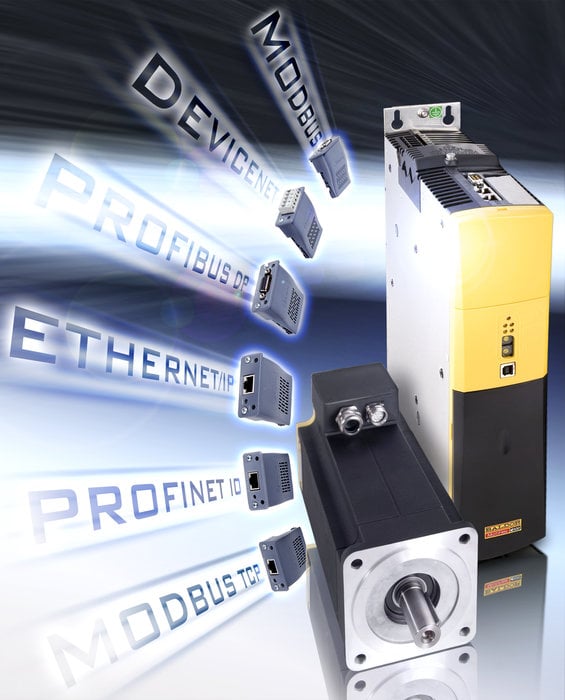
“We wanted to develop enhanced versions of our MotiFlex e100 three-phase drive ranges, able to communicate with any PLC and to comply more easily with industry Fieldbus systems. To do this, our strategy was to use a standardised solution rather than develop these interfaces in-house. We decided to do this because time to market was critical and because it is not our core competence to do that. But, we found a higher added value than expected in the HMS solutions” explains David Greensmith, Product manager at Baldor’s UK motion control centre.
Baldor's e100 AC drives, suitable for use in standalone motion control systems or networked systems, are now compatible with the Ethernet/IP, Modbus TCP and Powerlink industrial standards. Offering economic and space-saving solutions for many common single-axis automation requirements, the drives also feature an Ethernet interface compatible with the deterministic Ethernet-compatible motion control standard, Powerlink. The versatile drives may be used to control rotary and linear servo motors, linear motors, closed-loop vector motors, and in V/Hz control modes.
“This system is one of the very first of its kind: it integrates CANopen, it offers Real time Ethernet and it is highly adaptable to communication standards. Now, our new range provides system builders with a universal drive platform that can be used in many different ways to suit different customers and applications, from standalone motion control systems to networked systems hosted by PLCs or other devices. This solution simplifies automation for food, labelling, packaging, electronics, printing wood/metalworking and more”, adds David Greensmith.
The embedded Mint Lite capability is now being fitted without charge on all of Baldor's MicroFlex e100 and MotiFlex e100s. It supports a range of basic motion programming requirements including performing relative and absolute moves, S-ramp profiles, jog and homing movements, changing target positions on the fly, registration moves, and reacting to real-time trigger events. The programming facility allows standalone drives to provide solutions for many common automation and machinery tasks such as cutting or feeding to length, indexing axes, simple pick and place motion, and machine adjustments such as changing guides or backstops to reconfigure machinery for new batches. This capability is especially useful in Fieldbus interfacing, creating adaptability for the user to choose to use a standard drive control interface or optimise the process data and behaviour for the application.
Flexible, consistent and open communication modules
“The HMS Anybus advantage is that it provides a unified interface. The consistency of their range of product is unique. Thus, our engineering costs are reduced. We have the same kind of product for all different fieldbuses”, explains David Greensmith.
“We have studied the offers of 2 or 3 vendors, but in the end, the HMS solution was more consistent and more standardized. The HMS solutions were also very compact. It was a key issue for the smallest sizes of our drive range. Anybus-CC, the solution we have implemented, is also very simple to install”.
Anybus CompactCom (Anybus-CC) module is intended for OEM. It provides instant connectivity to all leading fieldbus, industrial Ethernet protocols, serial, USB and wireless networks without the need for any hardware and software changes to your automation device. Automation devices with an integrated Anybus-CC slot can use any Anybus-CC module. One module for a given network can simply be exchanged with another dedicated Anybus-CC module and be instantly connected to that network without the need for hardware and software changes in the automation device. Anybus-CC enables savings of up to 70% on development costs compared with in-house development. Standardized hardware and software interface independent of the network.
Another key issue was to allow for much more flexible communication with PLCs. Thanks to HMS our drives could be controlled with a PLC, using industry standards. With HMS we can interface with all major fieldbuses. As well as their own local input/output (I/O) and Canopen expansion, our drives also have option-card slots, providing configurability for specific applications including using Anybus-CC”.
“HMS is undoubtedly a partner for the future, because it offers flexibility to existing range and new generations of drives” concludes David Greensmith.
Baldor Electric is an American company, with Headquarters in Fort Smith, Arkansas. With 7000 people, a turn-over of $2B and 26 plants in the US, Canada, England, Mexico and China, this company is the unrivaled leader in the USA. Baldor sells its solutions through subsidiaries or distributors in more than 70 countries. Drives and control development is based in two locations, US headquarters and the UK facility.
“The company’s background is in Motion Control and Positioning for fairly complex systems” explain David Greensmith. “We have a leading position in intelligent drive programmability that’s built on flexibility and ease of use”.
92 people are employed in Baldor’s European headquarters in the UK, of whom 30 are involved in development.
More information: http://www.baldormotion.com/products/servodrives/overview.asp
Baldor's e100 AC drives, suitable for use in standalone motion control systems or networked systems, are now compatible with the Ethernet/IP, Modbus TCP and Powerlink industrial standards. Offering economic and space-saving solutions for many common single-axis automation requirements, the drives also feature an Ethernet interface compatible with the deterministic Ethernet-compatible motion control standard, Powerlink. The versatile drives may be used to control rotary and linear servo motors, linear motors, closed-loop vector motors, and in V/Hz control modes.
“This system is one of the very first of its kind: it integrates CANopen, it offers Real time Ethernet and it is highly adaptable to communication standards. Now, our new range provides system builders with a universal drive platform that can be used in many different ways to suit different customers and applications, from standalone motion control systems to networked systems hosted by PLCs or other devices. This solution simplifies automation for food, labelling, packaging, electronics, printing wood/metalworking and more”, adds David Greensmith.
The embedded Mint Lite capability is now being fitted without charge on all of Baldor's MicroFlex e100 and MotiFlex e100s. It supports a range of basic motion programming requirements including performing relative and absolute moves, S-ramp profiles, jog and homing movements, changing target positions on the fly, registration moves, and reacting to real-time trigger events. The programming facility allows standalone drives to provide solutions for many common automation and machinery tasks such as cutting or feeding to length, indexing axes, simple pick and place motion, and machine adjustments such as changing guides or backstops to reconfigure machinery for new batches. This capability is especially useful in Fieldbus interfacing, creating adaptability for the user to choose to use a standard drive control interface or optimise the process data and behaviour for the application.
Flexible, consistent and open communication modules
“The HMS Anybus advantage is that it provides a unified interface. The consistency of their range of product is unique. Thus, our engineering costs are reduced. We have the same kind of product for all different fieldbuses”, explains David Greensmith.
“We have studied the offers of 2 or 3 vendors, but in the end, the HMS solution was more consistent and more standardized. The HMS solutions were also very compact. It was a key issue for the smallest sizes of our drive range. Anybus-CC, the solution we have implemented, is also very simple to install”.
Anybus CompactCom (Anybus-CC) module is intended for OEM. It provides instant connectivity to all leading fieldbus, industrial Ethernet protocols, serial, USB and wireless networks without the need for any hardware and software changes to your automation device. Automation devices with an integrated Anybus-CC slot can use any Anybus-CC module. One module for a given network can simply be exchanged with another dedicated Anybus-CC module and be instantly connected to that network without the need for hardware and software changes in the automation device. Anybus-CC enables savings of up to 70% on development costs compared with in-house development. Standardized hardware and software interface independent of the network.
Another key issue was to allow for much more flexible communication with PLCs. Thanks to HMS our drives could be controlled with a PLC, using industry standards. With HMS we can interface with all major fieldbuses. As well as their own local input/output (I/O) and Canopen expansion, our drives also have option-card slots, providing configurability for specific applications including using Anybus-CC”.
“HMS is undoubtedly a partner for the future, because it offers flexibility to existing range and new generations of drives” concludes David Greensmith.
Baldor Electric is an American company, with Headquarters in Fort Smith, Arkansas. With 7000 people, a turn-over of $2B and 26 plants in the US, Canada, England, Mexico and China, this company is the unrivaled leader in the USA. Baldor sells its solutions through subsidiaries or distributors in more than 70 countries. Drives and control development is based in two locations, US headquarters and the UK facility.
“The company’s background is in Motion Control and Positioning for fairly complex systems” explain David Greensmith. “We have a leading position in intelligent drive programmability that’s built on flexibility and ease of use”.
92 people are employed in Baldor’s European headquarters in the UK, of whom 30 are involved in development.
More information: http://www.baldormotion.com/products/servodrives/overview.asp