www.industry-vietnam.com
08
'10
Written on Modified on
REMFORM screw reduce the cost of plastic components assembly
Remform screws from Arnold Umformtechnik GmbH & Co. reduce the overall assembly cost of plastic parts as they do not require nuts or inserts. They furthermore ensure the highest levels of assembly security, due to a specific design that creates a large difference between the forming torque and the stripping torque. The main application of REMFORM for plastic parts assembly is the automotive industry.
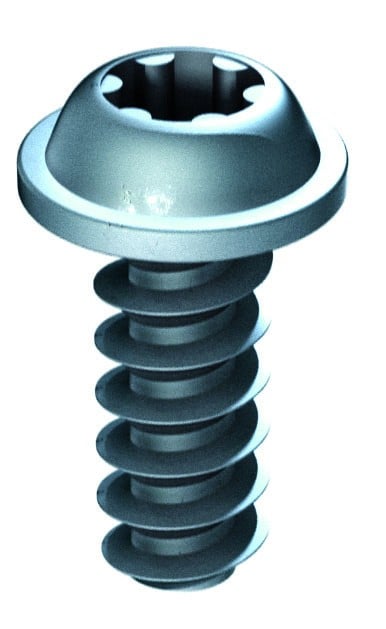
In contrast to other joining methods for plastic components, direct assembly with Remform screws does not require nuts or inserts to hold the components together. Remform screws form their own threads and the necessary core hole in the plastic component concerned. This automatically eliminates the need for cost-intensive processes involved in joint preparation. At the same time, the high threading speed required by the method reduces production times.
At the same time, Remform screws do not sacrifice anything when it comes to joint security. The asymmetrical thread geometry of the Remform design steers the resulting forces during the threading process in the desired direction. To improve material flow, the thread flank facing away from the head of the screw is radiused. The steep thread flank facing the head of the screw accommodates the displaced plastic and increases the thread flank overlap, which ensures high breakaway force for tension as well as torque. The large difference between the forming torque and the stripping torque provides an extra margin of safety, which is reflected in screws that are always fully tightened. Stripped threads are out of the question.
The resulting stripping torque and pull-out load, as well as the difference between the threading and stripping torques, are in some cases considerably more than 30% greater than the values with 30-degree low-angle screws.
At the same time, Remform screws do not sacrifice anything when it comes to joint security. The asymmetrical thread geometry of the Remform design steers the resulting forces during the threading process in the desired direction. To improve material flow, the thread flank facing away from the head of the screw is radiused. The steep thread flank facing the head of the screw accommodates the displaced plastic and increases the thread flank overlap, which ensures high breakaway force for tension as well as torque. The large difference between the forming torque and the stripping torque provides an extra margin of safety, which is reflected in screws that are always fully tightened. Stripped threads are out of the question.
The resulting stripping torque and pull-out load, as well as the difference between the threading and stripping torques, are in some cases considerably more than 30% greater than the values with 30-degree low-angle screws.