www.industry-vietnam.com
02
'09
Written on Modified on
3-D Hall Sensor Algorithm Developed in Maple Produces a More Efficient Washing Machine Design
Dr. Frank Allmendinger leads a research and development project team at Marquardt GmbH, a German company that develops and manufactures switches and switching systems. Over the last three years, his team designed an innovative three-dimensional load and imbalance sensor, which is used in a new washing machine model from a well-known company in the "white goods" sector.
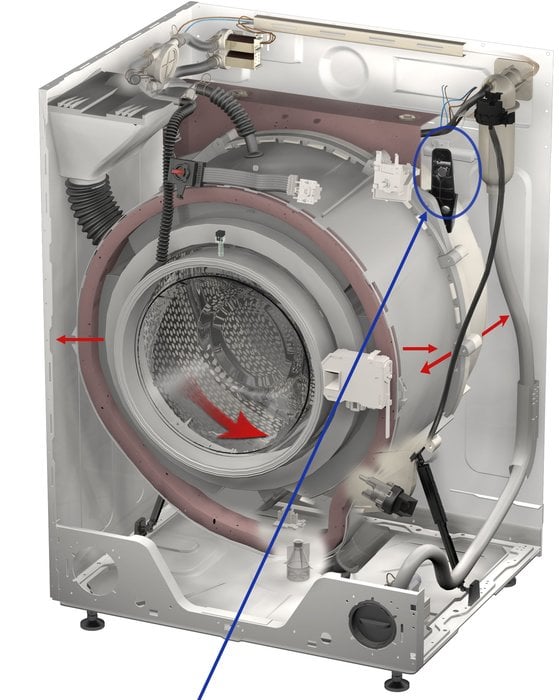
In industry, the trend is to move from washing machines with a drum capacity for 5 kg of laundry to larger ones with a capacity of 7 or 8 kg. However, these large drums are still being placed in the standard washing machine housing with a width of 60 cm, which means there is a much smaller space left between the drum and the housing. This means collisions are more probable. It is therefore necessary to measure the position of the drum relative to the housing, use this signal to identify impacts of the drum against the housing in advance, and react accordingly. Marquardt’s sensor was developed to detect the relative position in the three dimensions of the washing machine drum to the housing.
Having the ability to measure the drum position gives several other advantages; for instance, it is possible to sense imbalances and detect resonant frequencies of the mechanical system during the machine’s spin cycle. These imbalances can be reduced by slowing the rotation speed and distributing the weight more evenly. It even becomes possible to measure a load of clothing as it is placed into the machine and give a recommendation of how much detergent to use!
The Marquardt team, in close collaboration with the Fraunhofer Institute for Integrated Circuits, developed a new 3-D Hall sensor application specific integrated circuit (ASIC) that measures the three vector components of a dipole magnetic field. The complete measurement system consists of a magnet affixed to the drum in the washing machine and the 3-D Hall sensor ASIC attached to the unit housing. The Hall sensor measures both the direction and strength of the magnetic field, determining the relative movement of the magnet simultaneously in all three dimensions. This information is then communicated to the onboard microcontroller, which uses a proprietary algorithm to determine how to control the movement of the drum.
To develop the algorithm, the Marquardt group used Maple™. Dr. Allmendinger found Maple to be an invaluable tool, allowing him to work on complex problems such as modeling the magnetic fields, estimating the allowed tolerances for the magnet, and determining whether the tilt of the 3-D-Hall-Sensor module was within a very small tolerance of approximately two degrees. The resulting algorithm was translated to C code to run on the controller.
Dr. Allmendinger first worked with Maple while studying at university. He was impressed by Maple’s ability to work with symbolic mathematics, its powerful graphing tools, its technical document interface, and its export capabilities to other languages (such as C, MATLAB®, and Java™). Dr. Allmendinger said, “It was very simple to work in Maple, even with the complex mathematics involved. We found it quite easy to enter and modify equations, determine whether they had a solution, then go back and make necessary changes. I found Maple’s user interface very easy and smooth to work with; especially the export capabilities and interoperability with other technical programs have become much better, and it is now invaluable in rapid solution development.”
The new 3-D positioning algorithm in the Hall sensor yields several advantages. First, assembly is simple because there is no mechanical connection between the magnet and the sensor. As the measured values of the three magnetic field components can be recorded simultaneously, the sensor system also offers the option of calculating speed. Overall, the design enables natural resources to be handled more responsibly. The use of mathematic field modeling makes it possible to discard traditional 3-D mapping techniques and use a smaller, more cost-effective microcontroller. Also, fewer resources are used by creating the considerably smaller magnet.
Marquardt is currently discussing further applications of its 3-D sensor with other well-known customers. These applications include general position sensing in regular production and automation technology and multimedia interfaces in the automotive industry, such as the I-Drive system in a BMW™ vehicle. The company is also considering further development of this innovative sensor concept, extending its capabilities to determine not only the 3-D distance of a Hall sensor from a magnet but also the 3-D solid angle. For this sensor concept, it will be necessary to measure the magnetic field at two positions. This problem will involve a six-dimensional system of equations and Maple will also be used in the development of this project.
Having the ability to measure the drum position gives several other advantages; for instance, it is possible to sense imbalances and detect resonant frequencies of the mechanical system during the machine’s spin cycle. These imbalances can be reduced by slowing the rotation speed and distributing the weight more evenly. It even becomes possible to measure a load of clothing as it is placed into the machine and give a recommendation of how much detergent to use!
The Marquardt team, in close collaboration with the Fraunhofer Institute for Integrated Circuits, developed a new 3-D Hall sensor application specific integrated circuit (ASIC) that measures the three vector components of a dipole magnetic field. The complete measurement system consists of a magnet affixed to the drum in the washing machine and the 3-D Hall sensor ASIC attached to the unit housing. The Hall sensor measures both the direction and strength of the magnetic field, determining the relative movement of the magnet simultaneously in all three dimensions. This information is then communicated to the onboard microcontroller, which uses a proprietary algorithm to determine how to control the movement of the drum.
To develop the algorithm, the Marquardt group used Maple™. Dr. Allmendinger found Maple to be an invaluable tool, allowing him to work on complex problems such as modeling the magnetic fields, estimating the allowed tolerances for the magnet, and determining whether the tilt of the 3-D-Hall-Sensor module was within a very small tolerance of approximately two degrees. The resulting algorithm was translated to C code to run on the controller.
Dr. Allmendinger first worked with Maple while studying at university. He was impressed by Maple’s ability to work with symbolic mathematics, its powerful graphing tools, its technical document interface, and its export capabilities to other languages (such as C, MATLAB®, and Java™). Dr. Allmendinger said, “It was very simple to work in Maple, even with the complex mathematics involved. We found it quite easy to enter and modify equations, determine whether they had a solution, then go back and make necessary changes. I found Maple’s user interface very easy and smooth to work with; especially the export capabilities and interoperability with other technical programs have become much better, and it is now invaluable in rapid solution development.”
The new 3-D positioning algorithm in the Hall sensor yields several advantages. First, assembly is simple because there is no mechanical connection between the magnet and the sensor. As the measured values of the three magnetic field components can be recorded simultaneously, the sensor system also offers the option of calculating speed. Overall, the design enables natural resources to be handled more responsibly. The use of mathematic field modeling makes it possible to discard traditional 3-D mapping techniques and use a smaller, more cost-effective microcontroller. Also, fewer resources are used by creating the considerably smaller magnet.
Marquardt is currently discussing further applications of its 3-D sensor with other well-known customers. These applications include general position sensing in regular production and automation technology and multimedia interfaces in the automotive industry, such as the I-Drive system in a BMW™ vehicle. The company is also considering further development of this innovative sensor concept, extending its capabilities to determine not only the 3-D distance of a Hall sensor from a magnet but also the 3-D solid angle. For this sensor concept, it will be necessary to measure the magnetic field at two positions. This problem will involve a six-dimensional system of equations and Maple will also be used in the development of this project.
SENSOR.jpeg: Magnet and 3-D Hall Sensor ASIC.
WITH_IMBALANCE_SENSOR.jpeg: washing machine with an imbalance sensor, the distance between the drum to the housing can be measured in three dimensions.
MagnField1.jpeg: Simulation of a magnetized field on the steel back wall of a washing machine.
WITH_IMBALANCE_SENSOR.jpeg: washing machine with an imbalance sensor, the distance between the drum to the housing can be measured in three dimensions.
MagnField1.jpeg: Simulation of a magnetized field on the steel back wall of a washing machine.