www.industry-vietnam.com
17
'08
Written on Modified on
ALTIC uses MEROBEL electromagnetic braking to control wire tension on its tensioners
High-speed coil winding requires the use of a tensioner between the feed coil and the receiving coil (end product). Fine control and the trend towards using larger-diameter wires to meet the high demand for electrical equipment such as transformers means that tension control solutions are required which offer high torque density as well as easy torque control. ALTIC, inventor of the modern tensioner and a benchmark for the sector, has selected EMP electromagnetic brakes from MEROBEL for its entire electrical and electronic range.
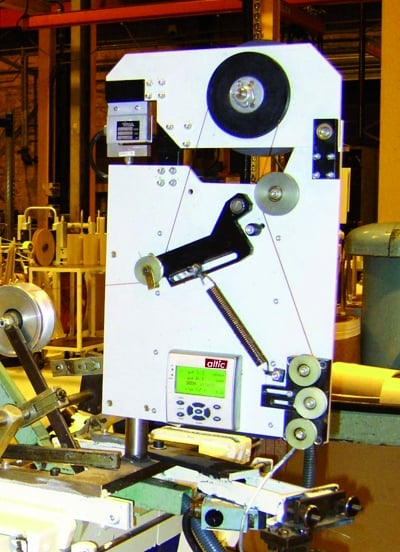
Today’s high-throughput production machines routinely attain speeds of more than 30 m/s for wires that are only a few hundredths of a millimetre in diameter. The forces applied to these wires are of the order of a few tenths of a newton, and must be controlled very precisely. The task is rendered even more complicated by the fact that the tension to be applied must be above the elastic limit of the wire (to give it rigidity) yet below its breaking point (to avoid any break leading to production shutdown).
It is obvious that at such speeds wire tension control cannot be applied at the feed coil, as its inertia is too high. The feed coil therefore remains static, and the wire is pulled by the tensioner and then wound on the receiving coil.
It is obvious that at such speeds wire tension control cannot be applied at the feed coil, as its inertia is too high. The feed coil therefore remains static, and the wire is pulled by the tensioner and then wound on the receiving coil.
It is easy to understand that in these conditions the precision of tension control during coil winding is a major issue.
Various braking technologies can be considered to control the torque applied to the shaft of the capstan/pulley around which the wire is wound (without slippage) to generate the winding tension.
Other than technologies based on friction brakes of various levels of sophistication, which cannot handle large-diameter wires, the solutions generally use motor control, but these are also generally limited to the finest wires for reasons of space and budget limitations.
But future developments are tending towards rather larger wire diameters, for example in order to meet the high demand from China and India for power transformers, but also for more specific applications in the cable industry.
Other than technologies based on friction brakes of various levels of sophistication, which cannot handle large-diameter wires, the solutions generally use motor control, but these are also generally limited to the finest wires for reasons of space and budget limitations.
But future developments are tending towards rather larger wire diameters, for example in order to meet the high demand from China and India for power transformers, but also for more specific applications in the cable industry.
In this context, ALTIC has selected MEROBEL EMP brakes for its entire range of electrical and electronic tensioners.
“We can only be pleased by the technical advantages provided by MEROBEL brakes for our most demanding applications,” states Jean-Yves Petitgas, director of ALTIC. “Their flexible, jerk-free operation, the very low electrical power needed for their control, the torque density and the robustness of the brakes are indispensable qualities for us. The technology of MEROBEL’s EMP brakes enables us to cover 100% of our current range.”
The electromagnetic brake works on the following principle: a change in the magnetic field alters the viscosity of the EMP powder, controlling the mechanical coupling between the inner and outer rotors. With this technique, the torque is proportional to the current that produces the magnetic field and is independent of the rotation speed. The torque/size ratio is better than for a friction-based mechanical solution. The torque is reliable and reproducible, without shocks, and the response time is rapid. Wear is also very low, giving a long maintenance-free lifetime.
Their design means that mechanical installation is generally very simple.
ALTIC uses the FAS and FRAS models (output-shaft brakes) for the smallest sizes and the FAT FRAT models (through-shaft brakes) for the rest of the range. In addition, ALTIC fits MEROBEL PowerBLOCK2 power supplies in all cases, ensuring very precise electrical control thanks to their closed-loop-controlled output current.
“We can only be pleased by the technical advantages provided by MEROBEL brakes for our most demanding applications,” states Jean-Yves Petitgas, director of ALTIC. “Their flexible, jerk-free operation, the very low electrical power needed for their control, the torque density and the robustness of the brakes are indispensable qualities for us. The technology of MEROBEL’s EMP brakes enables us to cover 100% of our current range.”
The electromagnetic brake works on the following principle: a change in the magnetic field alters the viscosity of the EMP powder, controlling the mechanical coupling between the inner and outer rotors. With this technique, the torque is proportional to the current that produces the magnetic field and is independent of the rotation speed. The torque/size ratio is better than for a friction-based mechanical solution. The torque is reliable and reproducible, without shocks, and the response time is rapid. Wear is also very low, giving a long maintenance-free lifetime.
Their design means that mechanical installation is generally very simple.
ALTIC uses the FAS and FRAS models (output-shaft brakes) for the smallest sizes and the FAT FRAT models (through-shaft brakes) for the rest of the range. In addition, ALTIC fits MEROBEL PowerBLOCK2 power supplies in all cases, ensuring very precise electrical control thanks to their closed-loop-controlled output current.
Discussions are in progress to optimize the characteristics of the MEROBEL digital tension controllers in the context of this particular use in order to extend their application to ALTIC’s most automatic tensioner range.
“The quality of our technical discussions and the accumulation of our overlapping experiences mean that we can look forward to the rapid introduction of solutions providing still further improvements in the performance and reliability of our equipment. This is invaluable help for continuing our commercial expansion to more distant areas, whether in Eastern Europe, the Americas or in Asian countries,” concluded Jean-Yves Petitgas.
ALTIC is the inventor of the modern wire tensioner. After 40 years, the company maintains its position as a worldwide benchmark for wire tensioners and a leader in innovation. ALTIC manufactures the only closed loop force control solutions available on the market. Based in southern France, ALTIC now exports almost 80% of its production.
“The quality of our technical discussions and the accumulation of our overlapping experiences mean that we can look forward to the rapid introduction of solutions providing still further improvements in the performance and reliability of our equipment. This is invaluable help for continuing our commercial expansion to more distant areas, whether in Eastern Europe, the Americas or in Asian countries,” concluded Jean-Yves Petitgas.
ALTIC is the inventor of the modern wire tensioner. After 40 years, the company maintains its position as a worldwide benchmark for wire tensioners and a leader in innovation. ALTIC manufactures the only closed loop force control solutions available on the market. Based in southern France, ALTIC now exports almost 80% of its production.